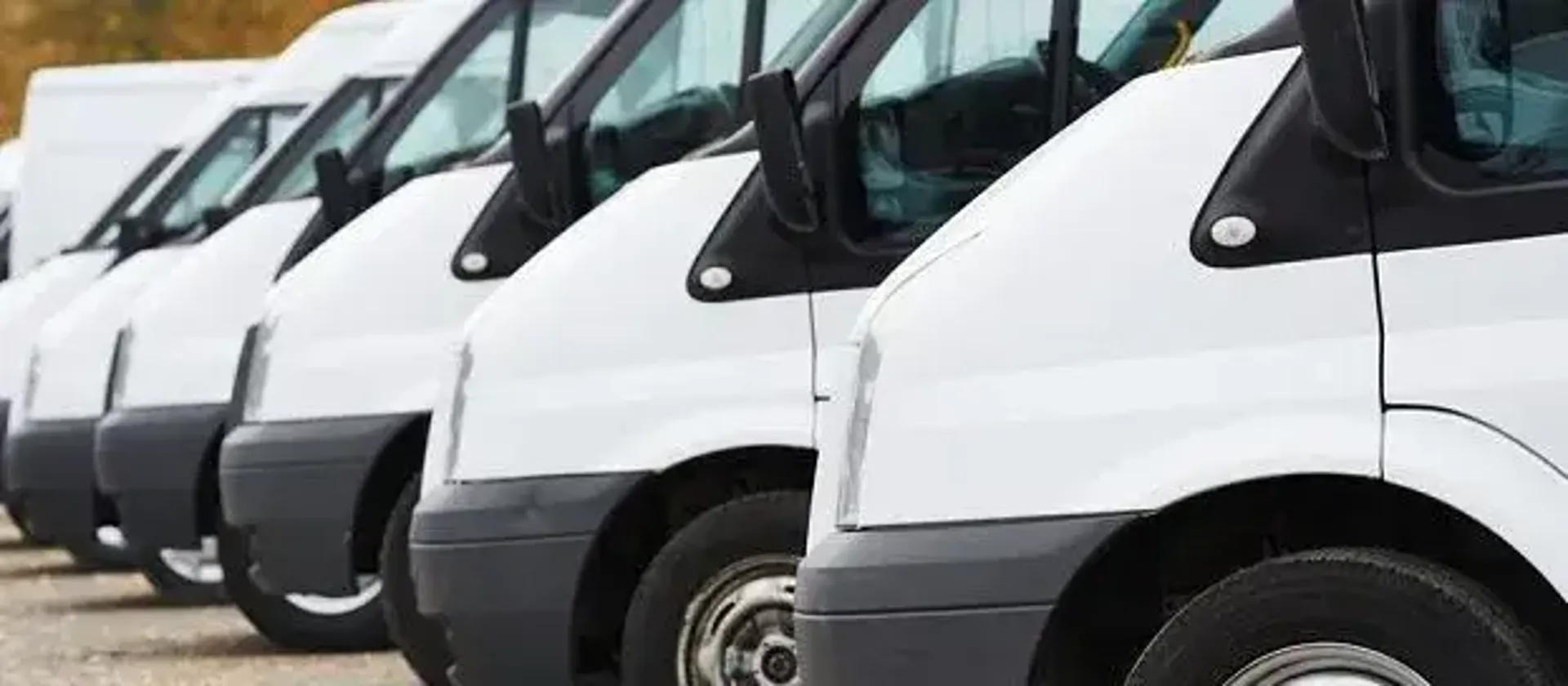
06/10/2015
Downtime has an impact on revenue, reputation and fleet management costs. Yet it remains a relatively un-measured contributing factor to the annual costs of running a business.
Partly, this problem is derived from the unpredictable nature of vehicle downtime: you cannot forecast when your drivers are going to have accidents. But accidents are not the only cause of vehicles being off the road. By concentrating on controllable contributing factors to downtime, costly periods of interrupted service can be measured, prevented and managed.
Prioritise your vehicles
In some industries, certain vehicles are more indispensable than others. First response vehicles in the emergency services, for example, are critical; while the car a station chief uses can safely be off the road without interrupting front-line service.
If your fleet includes vehicles without which your operation cannot run, these should be prioritised for non-scheduled repair. A prepared company works with its garage or leasing company to create a priority sheet detailing the order in which vehicles should be seen to, when they need attention that falls outside normal maintenance.
Plan your maintenance
Planned preventive maintenance (PPM) refers to routine servicing and MOTs. While it’s hard to manage unpredictable accidents or breakdowns, routine downtime is a known quantity. The key to good PPM management is to arrange a fleet PPM schedule that maximises the number of vehicles on the road without extending the periods between services. PPM will also help you limit the number of breakdowns you fall prey to by ensuring vehicle parts are replaced at the correct intervals, minimising extensive wear and tear.
Limit your speed
Speed limiters aren’t always popular with fleet drivers, but they can save fleet managers significant headaches. Driving within the speed limit reduces the risk of accidents, increases fuel efficiency and minimises impact on vehicle parts. Combined with a good PPM schedule, fitting speed limiters can have a real impact on the occurrence of breakdowns in your fleet.
Pick the right vehicle
Extra outlay when buying or leasing vehicles can repay itself in minimal downtime. A cheaper van or lorry may be unfit for purpose, particularly if it’s being asked to carry loads inappropriate to its gross weight, wheelbase or axle weight.
Extra or after-market vehicle specifications such as rev limiters or automatic gearboxes can further reduce the risk of unplanned downtime.
Reliable vehicles, fit for purpose and with known affordable maintenance and repair costs, will work within their limits, reducing mechanical stress and minimising the chances of breakdown.
Communicate with your garage
Whether it’s a planned service or an accident repair, your vehicle’s downtime should be governed by measurable deadlines. Communication with your workshop, lease company or service provider helps ensure a predictable journey from booking in to getting back on the road.
PPM booked well in advance (see ‘Plan your maintenance’, above) should have little to no effect on the daily running of your fleet. For accident and breakdown work, a service level agreement with your garage can define acceptable timeframes for diagnosis, part sourcing and repair.
Vehicle downtime isn’t always predictable, but with forward planning and preventive measures it can be managed. Managing it controls unnecessary costs - which for bigger operations can be measured in the thousands every day - and keeps your customer-facing services running without a break.
What steps are you taking to reduce vehicle downtime? Let us know on Twitter and LinkedIn.